Factors affect the sealing performance of butterfly valves
For the choice of butterfly valve, sealing is the most important attribute, because it directly affects the effect of butterfly valve throttling and is a direct manifestation of the quality of butterfly valve products. However, for most
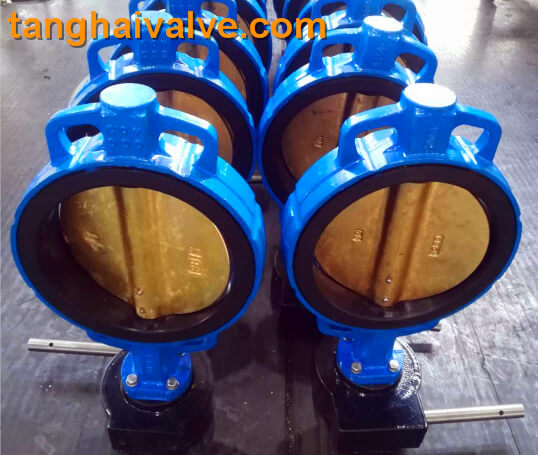
wafer type butterfly valve, NBR seat (11)
working conditions, sealing does not mean that one drop is not allowed to leak. For the sealing performance of the butterfly valve, the accurate judgment standard should be: any sealing is allowed to have a small amount of leakage sometimes, if the leakage is not effective, it can be considered as sealed. The use experience of the valve shows that, in many cases, it is unnecessary to put high requirements on the sealing performance of the valve, because some working conditions completely allow a small amount of leakage of the medium, because this leakage is not enough to affect the use of the valve.
Of course, there are also more demanding working conditions in terms of sealing, usually for high pressure or corrosive media, and pipelines that transport flammable, explosive and toxic media. The leakage of the medium between the valve sealing surfaces may cause personal hazards, economic losses, and even In the event of an accident, etc., the tightness requirements should be reasonably put forward according to the danger level of the medium.
For example, for a hard-sealed butterfly valve, a certain amount of leakage is allowed when the sealing performance test is performed in the closed state in accordance with the technical standards for valve manufacturing. However, in order to ensure the high sealing performance of the hard-sealed butterfly valve, Tanghai Valve still carefully grinds the sealing surface, increasing the specific pressure on the sealing surface within the allowable specific pressure range of the sealing surface material, and improving the rigidity of the structure at the same time. At the same time, Tanghai Valve has stricter requirements on design, manufacturing and processing, such as:
(1) The quality of the valve body and bonnet, especially during forging or casting, should avoid defects and uneven composition such as folding, slag inclusion, pores, organization evacuation, and hidden cracks.
(2) The processing quality of the connecting parts of the valve stem and the valve body is improved, especially the roughness of the valve stem and the stuffing box, the straightness of the valve stem, the verticality of the stuffing box hole of the bonnet, and the processing accuracy are increased.
(3) The structure selection of the valve stuffing box. Since the seal at the valve stem is a dynamic seal, the packing is easy to wear during the rotation or sliding process of the valve stem. It is necessary to select a special low-leakage packing seal and packing seal combination, and strictly control the packing and packing. The gap between the valve stem, the gap between the packing and the stuffing box.
In summary, in addition to meeting the process conditions and standard specifications, the sealing performance of the control butterfly valve should also be fully considered for various operating conditions. In the engineering design, the sealing level of the butterfly valve should be selected to meet the principles of safety, reasonableness and economy.
TH Valve is a professional manufacturer of butterfly valve, gate valve, check valve, globe valve, knife gate valve, ball valve with API, JIS, DIN standard, used in Oil, Gas, Marine industry, Water supply and drainage, fire fighting, shipbuilding, water treatment and other systems, with Nominal Diameter of DN50 to DN1200, NBR/EPDM/VITON, Certificates & Approvals: DNV-GL, Lloyds, DNV, BV, API, ABS, CCS. Standards: EN 593, API609, API6D
Related news/knowledge:
Cryogenic valve principle |standard |illustration |selection
What are the main factors affecting valve sealing?
Factors Affecting the Operation and Use of resilient seated Butterfly Valves
The difference of cryogenic valve and ordinary temperature valve