Ball valve installation and maintenance methods
Ball valve installation:
1. It must be confirmed that the pipeline and valve have been cleaned before operation.
2. The actuator operation of the valve drives the valve stem to complete rotation according to the size of the input signal: when it rotates 1/4 turn (900) in the forward direction, the valve is closed. When the reverse rotation is 1/4 turn (900), the valve opens.
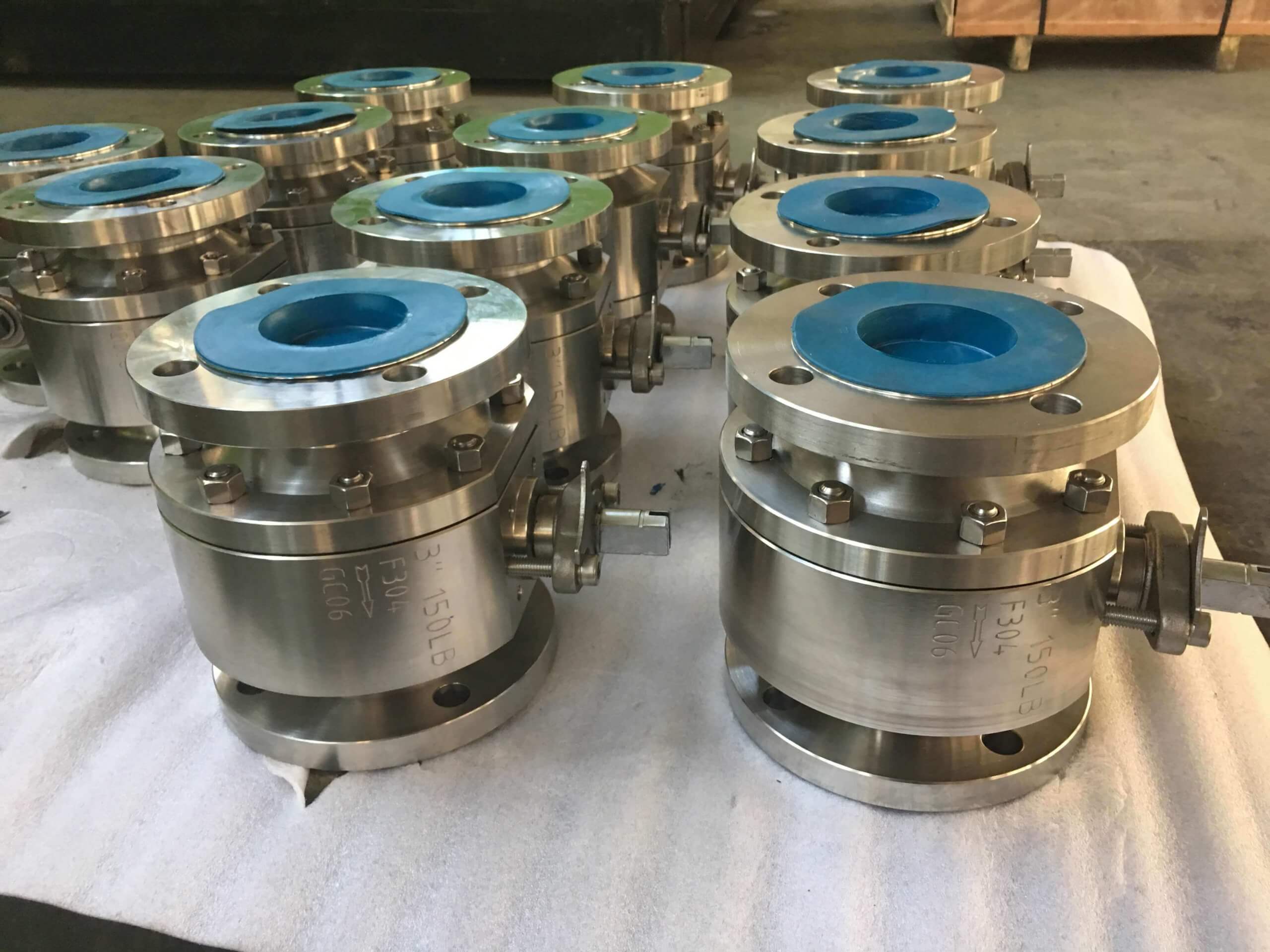
fixed ball valve
3. When the direction indicator arrow of the actuator is parallel to the pipeline, the valve opens; when the arrow is perpendicular to the pipeline, the valve closes.
Ball valve repair:
Longer service life and maintenance-free time will depend on several factors: under normal working conditions, maintaining a harmonious temperature/pressure ratio, and reasonable corrosion data. Note: When the ball valve is closed, the fluid pressure in the valve body It still exists. Before maintenance, remove the pipeline pressure and leave the valve in the open position. Before maintenance, disconnect the power supply or air supply. Before maintenance, disconnect the actuator from the bracket.
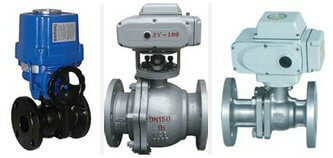
electric ball valve
1. Packing lock If the packing culvert is slightly leaking, the valve stem nut must be locked. Note: Do not lock, usually lock 1/4 ring to 1 ring, the leakage will stop.
2. Replace the valve seat and seal
A. Disassembly Keep the valve in the half-open position to flush out the dangerous substances that may exist inside and outside the valve. Close the ball valve, remove the bolts and nuts of the flanges on both sides, and completely remove the valve from the pipeline. Disassemble the drive device-actuator, connecting bracket, lock washer, stem nut, butterfly shrapnel, glam, wear-resistant sheet, stem packing in order. Remove the body cover connecting bolts and nuts, separate the valve cover from the valve body, and remove the valve cover gasket. Make sure that the valve ball is in the “off” position. This will make it easier to take it out of the valve body, and then remove the valve seat. Gently push the valve stem down from the hole in the valve body until it is completely taken out, and then take out the O-ring and packing ring. Note: Please operate carefully to avoid scratching the surface of the valve stem and the packing seal of the valve.
B. Reassembly Clean and inspect the parts under investigation. It is strongly recommended to replace the valve seat and bonnet gaskets and seals with spare parts kits. Reverse the order of disassembly and assembly. Use the specified torque to tighten the flange bolts crosswise. Tighten the nut with the specified torque. After installing the actuator, rotate the valve stem to drive the valve core to rotate the corresponding input signal to make the valve open and close. If possible, after installing the pipeline, test the sealing pressure and performance of the valve according to the standard.
Related knowledge: The role of the ball valve The working principle of the ball valve
TH Valve is a professional manufacturer of butterfly valve, gate valve, check valve, globe valve, knife gate valve, ball valve with API, JIS, DIN standard, used in Oil, Gas, Marine industry, Water supply and drainage, fire fighting, shipbuilding, water treatment and other systems, with Nominal Diameter of DN50 to DN1200, NBR/EPDM/VITON, Certificates & Approvals: DNV-GL, Lloyds, DNV, BV, API, ABS, CCS. Standards: EN 593, API609, API6D
Related news /knowledge:
Electric flange ball valve installation instructions;
Installation and maintenance of electric ball valve;
Installation and maintenance of electric ball valve;
Valves’ sealing requirements and daily maintenance;