electric wafer butterfly valve vs electric flange butterfly valve
The difference and selection of electric wafer butterfly valve and electric flange butterfly valve
As one of the most common valves in pipelines, electric butterfly valves are used to realize the on-off and flow control of various media in the pipeline system. They have been widely used in many fields such as petroleum, chemical industry, metallurgy, and hydropower. application. Then in the commonly used electric butterfly valve, it can be
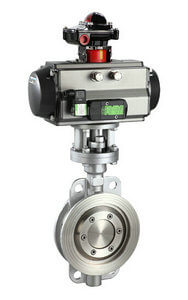
D673H-16C-stainless steel pneumatic triple eccentric butterfly valve
divided into two kinds, electric wafer butterfly valve and electric flange butterfly valve, and these two kinds of valves have their own characteristics, and they are not the same in performance. They can be used in Different industries.
For these two kinds of valves, in addition to the different structural forms, if they are under the same parameters, the biggest difference is that the connection method is different, that is, the installation form is different, which depends on the site working conditions!
The difference between electric wafer butterfly valve and electric flange butterfly valve:
The thickness of the electric wafer butterfly valve is relatively thin compared to the flanged butterfly valve. There are no flanges at both ends of the valve body, but only a few guide bolt holes. The valve uses a set of bolts/nuts to connect with the flange of the pipe end, which is generally applicable. It is used in places where the space is relatively narrow or the pipeline is restricted. The advantage is that it is more convenient to disassemble, the valve cost is lower, and the space is small, but the disadvantage is that one sealing surface has a problem, and both sealing surfaces have to be disassembled!
Electric flange butterfly valve has flanges at both ends of the valve body, which are connected with pipeline flanges. Compared with wafer butterfly valves, the sealing performance is more reliable. It is generally used in places with larger diameters or higher pressures, but the cost is relatively good.
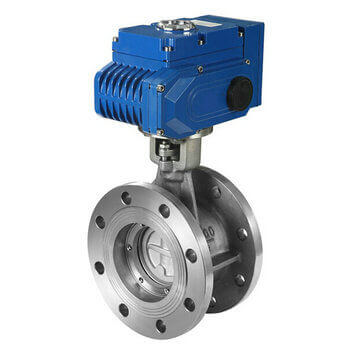
D943H-16C-metal seated stainless steel electric triple offset butterfly valve
Choice between the two:
However, there are still some things to pay attention to in the design. For example, wafer type valve bolts are generally relatively long. Under high temperature conditions, the expansion of the bolts may cause leakage, so it is not suitable for large pipe diameters under high temperature conditions. . Another example is the wafer butterfly valve generally cannot be used in the end of the pipeline and downstream needs to be disassembled, because when the downstream flange is removed, the wafer valve will fall off, in this case, it must be shortened separately. The flange type butterfly valve does not have the above problems, but the cost will be higher.
Related Electric butterfly valve series products View other butterfly valves
TH Valve is a professional manufacturer of butterfly valve, gate valve, check valve, globe valve, knife gate valve, ball valve with API, JIS, DIN standard, used in Oil, Gas, Marine industry, Water supply and drainage, fire fighting, shipbuilding, water treatment and other systems, with Nominal Diameter of DN50 to DN1200, NBR/EPDM/VITON, Certificates & Approvals: DNV-GL, Lloyds, DNV, BV, API, ABS, CCS. Standards: EN 593, API609, API6D
Related news /knowledge:
What is a wafer type butterfly valve;
Wafer type double disc swing check valve introduction;
Comparison and analysis of the performance of the wafer butterfly valve;