Common leakage problems and remedies of resilient-seated gate valves
The resilient seated flange gate valve is an updated product of the gate valve, because the gate plate is wrapped by elastic materials such as rubber or PTFE, or the valve seat is made of elastic material. In short, one of the valve seat and the valve plate can be regarded as soft seal. The combination of soft and hard sealing can achieve zero leakage. And because the connection form is flange connection, hence the name. It is widely used in fluid pipelines such as
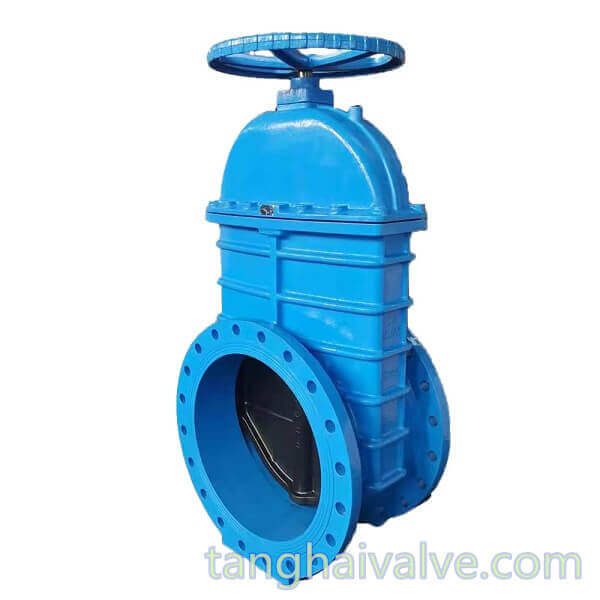
AWWA C509-C515-resilient seated gate valve-DN600-150lb (2)
tap water, sewage, construction, petroleum, chemical industry, food, medicine, textile, electric power, shipbuilding, metallurgy, energy system, etc. The soft sealing flange gate valve is characterized by low fluid resistance, wide applicable pressure and temperature range, unlimited medium flow direction, and good sealing performance.
In procurement, the leakage inspection of resilient seated flange gate valves is always the first concern. understand the product’s tightness, we first understand which components of the gate valve are prone to leaks, so that we can achieve good prevention and remedial measures. details as follows:
1. Leakage occurs at the junction of the gate valve and the gate valve
If this happens, first check whether the connecting bolts between the gate valves are tightened. This is to ensure that the inner gasket ring is fully integrated with the flange sealing groove surface. If a leak has occurred here, you can check the bolts and nuts in order and tighten them to the compression seal ring. Finally, check the size and accuracy of the gasket ring and the flange sealing groove surface, whether there is a bit of corrosion, sand holes, sand holes or impurities, and corresponding repair welding, repair or cleaning according to the situation.
2. The valve cover is leaking
Valve cover leakage is usually caused by the leakage of packing seals. If there is such a problem with the seal, you can check the selection first. If the selection of the seal and the sealing groove do not match, it is easy to leak. This problem can be solved by replacing the sealing ring or repairing the sealing groove. The appearance of burrs, fracturing, twisting, etc. of the seals may also cause leakage and need to be replaced in time. Finally, check whether the sealing surface of each sealing groove is rough or have other defects. If there are defects, remove the defects or update the damaged parts. Special attention should be paid to the packing installation situation and the matching surface of the packing seal. To check the installation of these packings, it is found that the upper and lower packings are installed upside down and need to be removed and reinstalled according to the correct method.
3. Leakage on the surface of the valve body cavity
In this case, the valve body may have sand holes, sand holes and other casting defects during the casting process, which are difficult to be found before the pressure test. But once pressure is applied, leakage will occur in these places. This kind of problem is to be repaired, repaired or updated.
4. Leakage at the valve seat gate
This is also a relatively common leakage phenomenon. There are two cases of leakage of the sealing surface and leakage of the root of the sealing ring. We can start by checking the accuracy of the sealing surface. It is too rough and needs to be removed and reground. Secondly, check whether the sealing surface has defects such as pitting, indentation, blisters, cracks, etc., and pay attention to the replacement of the gate or valve seat. Sometimes some valve seats with compression springs will leak due to the weakening of the compression spring’s elasticity. In addition, attention should be paid to whether the T-shaped connection between the valve plate and the valve stem is too loose. If there is a slope, it should be adjusted to its better size immediately.
5. Leakage caused by the entry of debris
If foreign matter such as welding slag, iron filings, impurities enter the valve body, it will also cause the valve plate to close to the expected depth and cause leakage. In this case, the valve body must be removed and cleaned.
6. Leakage caused by improper installation of valve seat
Special tools should be used to install the valve seat. If the valve seat is not installed in place, leakage will occur.
TH Valve is a professional manufacturer of butterfly valve, gate valve, check valve, globe valve, knife gate valve, ball valve with API, JIS, DIN standard, used in Oil, Gas, Marine industry, Water supply and drainage, fire fighting, shipbuilding, water treatment and other systems, with Nominal Diameter of DN50 to DN1200, NBR/EPDM/VITON, Certificates & Approvals: DNV-GL, Lloyds, DNV, BV, API, ABS, CCS. Standards: EN 593, API609, API6D
Related news/knowledge
Problems Existing in the Use of Triple Eccentric Butterfly Valves
7 types of flange sealing surface: FF, RF, M, FM, T, G, RTJ
Classification and features of Eccentric butterfly valves
Solution for accidental fall off of the valve plate of rising stem wedge gate valve