The difference between fixed ball valve and floating ball valve
There are many types of ball valves, such as hard-sealed ball valves, soft-sealed ball valves, welded half-ball valves, V-shaped ball valves, flanged ball valves, wafer ball valves, fixed ball valves, and floating ball valves. These classifications are based on the actual use of the manufacturer and the actual situation of the customer. Need, it is slowly researched and developed, but no matter how it develops, it is inseparable from the design principle of the ball valve. The so-called new product of the ball valve, no matter what kind of ball valve is developed, the principle and design plan are designed around the main body of the ball valve. The principles and standards come.
Here, we mainly talk about fixed ball valves and floating ball valves.
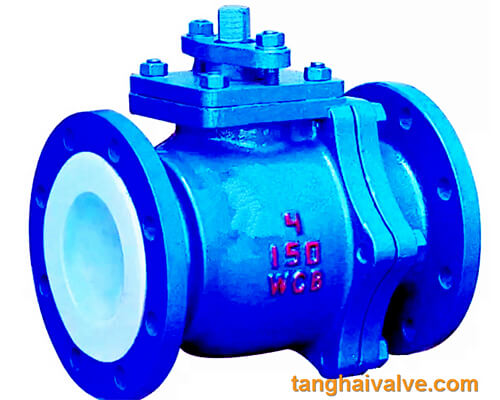
14 ball-valve-6
The more intuitive difference between the fixed ball valve and the floating ball valve is that the fixed ball valve is located at the lower end of the valve, and there is a stem supporting hole corresponding to the upper stem. The upper and lower stems firmly fix the spool of the ball valve to make the spool of this valve. Can not roll at will. The sealing principle is that the valve seats on both sides are pressed against the fixed ball core in the middle, so that the valve has a sealing function.
The soft sealing ball valve is round at the lower end of the valve without opening. The ball core is only fixed unilaterally by the upper stem. The ball core can move freely inside the valve cavity. When sealing, the valve seats on both sides of the ball valve are fixed. The valve seat is pressed by the valve core to produce a sealing effect.
Generally speaking, fixed ball valves are suitable for large diameters and high pressure ball valves when the pressure is relatively high. The soft-sealed ball valve is suitable for small caliber, and is suitable for low-pressure sealing ball valve when the pressure is relatively low.
The main feature of the floating ball valve is that the ball has no supporting shaft. The ball is supported by the valve seats at the inlet and outlet ends of the valve. The valve stem and the ball are movably connected. The ball of this ball valve is held in a “floating state” by two valve seats.
The ball can freely rotate between the two valve seats through the valve stem by means of a handle or other driving device.
When the flow channel hole of the ball is aligned with the valve channel hole, the ball valve is in an open state, the fluid is unblocked, and the fluid resistance of the valve is small. When the ball is rotated by 90°C, the flow channel hole of the ball is perpendicular to the valve channel hole, and the ball valve is in a closed state. Under the action of fluid pressure, the ball is pushed to the valve seat at the outlet end of the valve (referred to as the back of the valve) to make it press Tighten and ensure sealing.
Features of floating ball valve:
Under the action of the pressure difference, the ball will move slightly downstream of the valve;
The sealing performance of the ball valve mainly depends on its downstream valve seat;
The valve seat cannot move between the ball and the valve body.
Features of fixed ball valve:
The ball of the fixed ball valve is connected with the upper and lower stems as a whole, or made into an integral connecting ball, that is, the ball is forged (welded) with the upper and lower stems and mounted on the bearing. The ball can be aligned with the valve channel. The vertical axis rotates freely, but cannot move along the channel axis.
Therefore, when the fixed ball valve is working, all the force generated by the fluid pressure in front of the valve on the ball is transmitted to the bearing, and the ball will not move to the rear valve seat, so the valve seat will not bear excessive pressure, so the fixed ball valve The torque is small, the deformation of the valve seat is small, the sealing performance is stable, and the service life is long. It is suitable for high pressure and large diameter occasions.
Function of fixed ball valve
The function of preventing the valve stem from blowing out
Double cut and bleed (DBB) function
Safety function (fire protection function)
The function of injecting sealing grease when the valve leaks
Piston effect of ball valve seat (two-way piston effect of G series ball valve)
The purpose of the two-way piston effect: automatically release the pressure in the cavity of the valve body.
The use of the one-way piston effect: After the upstream valve seat is damaged, the fluid flows into the middle cavity, and the pressure in the middle cavity is higher than the pressure downstream of the valve.
Floating ball valve design should focus on the medium load to be considered in the material of the sealing ring. Excessive medium pressure will affect the life of the valve seat, and the ball can only have a slight offset. Therefore, the floating ball valve is generally suitable for DN200 or below DN200. The ball of the fixed ball valve whose nominal pressure does not exceed CLASS600Lb (10.0MPa) is fixed in the middle of the valve body by the upper and lower stems, and will not move after being pressed. The sealing of the fixed ball valve is to ensure the sealing by providing sufficient pre-tightening force through the leaf spring or cylindrical compression spring on the sealing valve seat, which is a double-sided forced sealing. The ball is supported by the upper and lower bearings, reducing friction, eliminating the excessive torque caused by the huge sealing load formed by the imported pressure pushing the ball and the sealing seat, and the operation is labor-saving. The fixed ball valve is double-sided and sealed on both sides, which will form a sealed cavity between the two sealed valve seats. To avoid danger, the fixed ball valve must be designed with an automatic pressure relief function, that is, when the pressure of the stagnant medium in the valve cavity increases abnormally and exceeds the spring At the time of pre-force, the valve seat retreats away from the sphere to achieve the effect of automatic pressure relief. After pressure relief, the valve seat automatically recovers. The fixed ball valve is widely applicable to various process pipelines with large diameter and high pressure due to its structural characteristics. Due to the need to assemble the upper and lower stems, only ball valves with a nominal diameter of DN50 or above can be produced. The nominal diameter is too small to be assembled.
Structure of fixed ball valve
1). Sphere
After introducing the various structural forms of the seal seat, I came to observe the ball structure of the same ball valve. The most important feature of the Tongding ball valve is that the ball does not deviate from the center of the sphere during the process of storing and opening. The ball I: the design of the pivot has three structural forms:
① the upper part of the sphere has a shaft, and the lower part is a shaft hole for a fixed shaft to insert. The structure of the sphere is a shaft and a hole structure.
② there are two upper and lower shaft holes on the sphere, which are inserted by the upper shaft and the lower shaft respectively. The structure is suitable for small diameters. The insertion depth of the hole is short, and it can only bear a small medium force. The structure is suitable for large diameters, can bear a large medium force, and the supporting journal is separated from the drive shaft. The drive shaft only bears the effect of torque.
③ there are two extending shafts on the sphere, two supporting plates vertically up and down. The medium force is transmitted to the valve body through the journal and the supporting plate. Similarly, the drive shaft only bears a single rotation. The moment action separates the medium force and the operating moment.
2). the valve body
Since the valve body is a forged cylinder, there is no usual valve neck. The valve neck is replaced by a stuffing box. The stuffing box is fixed on the platform of the valve body by bolts. The shaft seal is made of O-shaped rubber ring. The connecting support plate of the valve is also fixed on the valve body through the through hole on the stuffing box. It can be seen that the strength of the valve body in the journal part of this cylindrical structure is greatly weakened.
As for the structure of the valve body, like the floating ball valve, there are two types: side-mounted and top-mounted.
The side-mounted type can be divided into two sections, a main valve body and a secondary valve body structure, or a three-section type, a main valve body and two secondary valve body structures.
The top-mounted valve body is an integral structure. The upper valve cover uses bolts to form a complete pressure boundary with the valve body. The ball is a ball with upper and lower support shafts. The lower support bearing is embedded in the valve body, and the upper support bearing is placed in the valve cover. , The upper shaft end is machined with a groove connected to the flange of the shaft head to transmit torque. The medium force acts on the bearing. The drive shaft only transmits torque. It is designed as a blow-out prevention structure. The design of the valve seat The difficulty of assembly or disassembly is that the valve seat must move to both sides when the ball is installed in the valve cavity. In this way, a slidable back valve seat is designed. The valve seat is retracted into the left and right channels in advance. After the ball is installed, pass the back The flange on the valve pushes the valve seat to the center of the ball, and then uses a snap ring to snap into the groove of the back valve seat. When disassembling, first take out the snap ring, and then push the valve seat into the left and right sides of the valve cavity. In the right channel, the sphere can be taken out from the upper part. Therefore, the top-mounted structural ball has the advantage of being able to be repaired online.
Related types of valves:
We can also produce gate valve, check valve, globe valve, knife gate valve with API, JIS, DIN standard, used in Oil, Gas, Marine industry, Water supply and drainage, fire fighting, shipbuilding, water treatment and other systems, with Nominal Diameter of DN50 to DN1200, NBR/EPDM/VITON, Certificates & Approvals: DNV-GL, Lloyds, DNV, BV, API, ABS, CCS. Standards: EN 593, API609, API6D,