The difference between fluoroplastics PTFE and PFA
With the gradual popularity of PFA in the market, more and more customers are beginning to contact and understand this new material. Although I have a preliminary understanding, I am not very familiar with it. Customers still have many questions about this material. Recently, customers often ask about the difference between “soluble polytetrafluoroethylene (PFA)” and “polytetrafluoroethylene (PTFE)” for this new material. Today, we will briefly explain here:
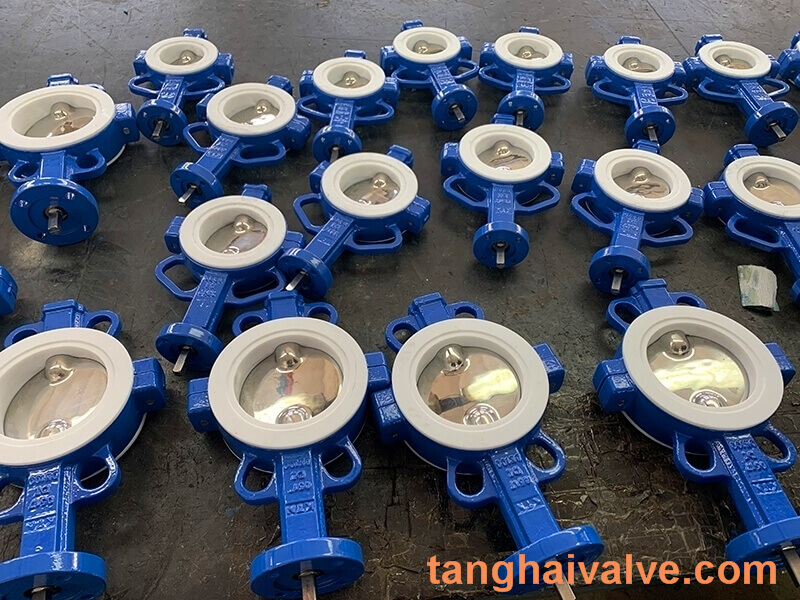
Fluorine lined butterfly valve-PTFE-WAFER (4)
The first is the difference in chemical structure:
PFA has added perfluoroalkoxy, which is equivalent to replacing one fluorine atom in PTFE with perfluoroalkoxy. A carbon is directly connected to an oxygen, and then the oxygen is connected to a group such as perfluoromethyl or perfluoroethyl. Compared with PTFE, the melt viscosity is reduced to facilitate processing. The other properties are not much worse than PTFE.
The second is the difference between applications:
PFA-has the same excellent properties as polytetrafluoroethylene, and has good thermoplasticity. It can be processed by ordinary thermoplastic resin processing methods. It is made by copolymerization of tetrafluoroethylene and perfluoropropyl vinyl ether in a certain proportion in an aqueous medium containing perfluorocarboxylate dispersant and persulfate initiator. It is a white translucent particle. It not only has the same operating temperature as PTFE, but also has better mechanical strength (about 2 to 3 times) at 250°C, and has excellent stress crack resistance. It has a wide processing range and good molding performance, and is suitable for molding processing such as compression molding, extrusion molding, injection molding, and transfer molding. It can be used to make wire and cable insulation sheaths, high frequency and ultra high frequency insulation parts, chemical pipelines, valves and pumps corrosion-resistant lining; special parts for machinery industry, various anti-corrosion materials for light and textile industry, PTFE anti-corrosion
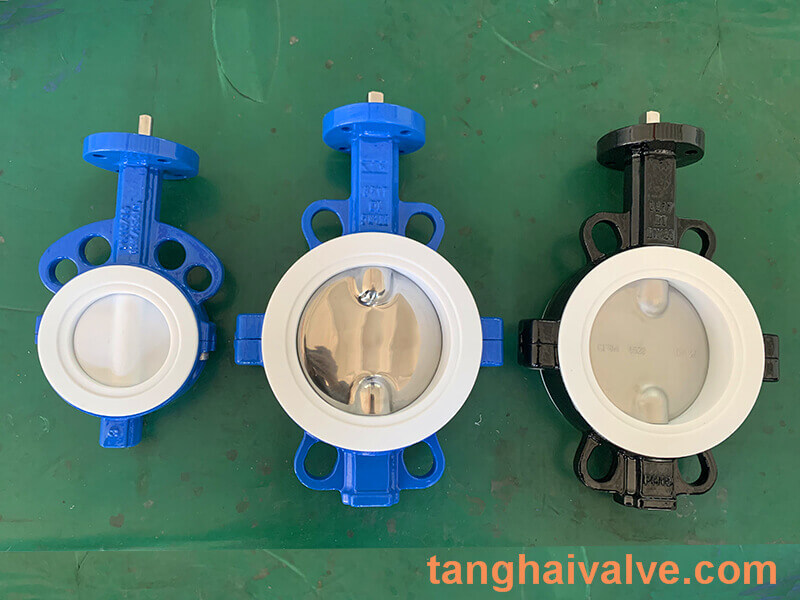
Fluorine lined butterfly valve-PTFE-WAFER (8)
lining Wait for the electrode. It is made by extruding meltable polytetrafluoroethylene pellets, with translucent milky white appearance, smooth surface, and dense and uniform cross-section. It is specially used for welding PTFE plates and tubes, so that PTFE products with simple shapes can be welded into products with complex shapes and larger sizes. The aqueous dispersion is a copolymer obtained by copolymerizing tetrafluoroethylene and perfluoropropyl vinyl ether, adding an emulsifier, and concentrating at a certain temperature. The solid content is 30%±1%. The appearance is milky white or light yellow translucent. It has various excellent properties of fusible polytetrafluoroethylene resin. It can be used for a long time at 260℃, and developed into advanced coatings with its excellent anti-sticking, anti-corrosion and easy processing properties. It can be sprayed and dipped, and is widely used in copy technology and food industry as anti-stick and anti-corrosion materials.
PTFE-Polytetrafluoroethylene is made by polymerizing tetrafluoroethylene monomer by suspension method or dispersion method. Molecular weight=5.2×105-4.5×107. White powder, 400 mesh accounted for 75%, tasteless, non-beauty and non-toxic. The relative density is 2.1-2.3, the refractive index is 1.37, the glass transition temperature is 327℃, and the thermal decomposition temperature is 415℃. Above 400°C, there is a slight weight loss and decomposes toxic gases. Use temperature -250~260 ℃, use at 210 ℃ up to 10000h. Excellent chemical resistance, resistance to any strong acid (including aqua regia), strong alkali, grease, insoluble in any solvent, very low friction coefficient, good wear resistance, and self-lubricating. Excellent aging resistance. Excellent electrical performance, good arc resistance. It is non-sticky, almost all sticky substances cannot adhere to its surface, and it is completely non-flammable. Known as the “Plastic King”. Tensile strength (MPa)>23 and elongation (%)>250.
Again, the difference in processing methods:
The main difference in processing methods is that PFA can be processed by hot melt injection molding, while PTFE cannot be processed by hot melt injection molding.
The above is the introduction to the difference between PFA and PTFE materials. For a long time in the past, PTFE has been sought after by the industry because of its superior physical and chemical properties. However, the limitations of its processing methods have made many scientists and engineers distressed. Finally, after PFA was launched on the market, it received new enthusiasm in the plastics industry. This kind of performance is similar to PTFE material, has very good processing performance, so that engineers’ problems can be easily solved. While PFA materials are gradually being widely used, I also hope that scientists can develop more advanced and superior materials to meet market needs.
TH Valve is a professional manufacturer of butterfly valve, gate valve, check valve, globe valve, knife gate valve, ball valve with API, JIS, DIN standard, used in Oil, Gas, Marine industry, Water supply and drainage, fire fighting, shipbuilding, water treatment and other systems, with Nominal Diameter of DN50 to DN1200, NBR/EPDM/VITON, Certificates & Approvals: DNV-GL, Lloyds, DNV, BV, API, ABS, CCS. Standards: EN 593, API609, API6D