What are the main factors affecting valve sealing?
Valve leakage is very common in daily life and industrial production, and the impact is very large. It will cause waste or bring danger to life. For example, the leakage of tap water valve will lead to serious consequences, such as the
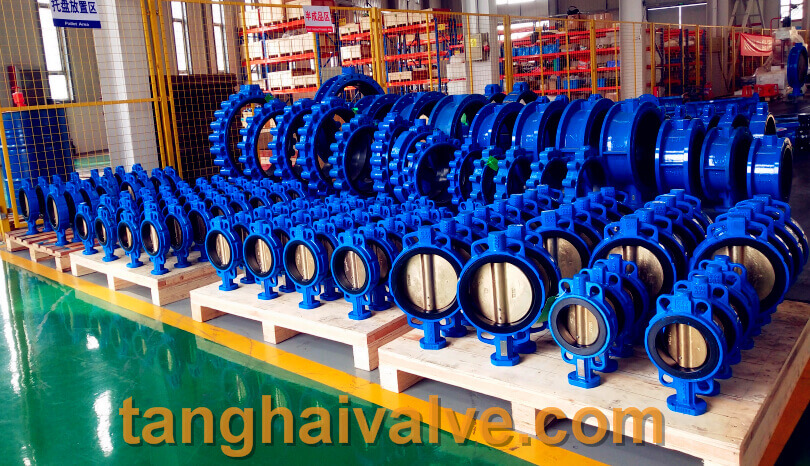
ductile iron, DI, butterfly valve, manufacturer, center line, TH valve
chemical industry. Toxic, harmful, flammable, explosive and corrosive media leakage, etc., serious threats to personal safety, property safety and environmental pollution accidents. A valve that relies on external force to rotate and drive to open and close is designed with a sealing device. It is used to install a certain number of packing seals in the packing culvert to achieve a sealing effect, but how about the sealing? Leakage at the packing of the valve is one of the most prone to leakage failure in the valve, but the reasons are largely the following reasons.
1. The structure of the sealing pair
The structure of the sealing pair will change when the temperature or sealing force changes. Moreover, this change will affect and change the mutual force between the sealing pairs, thereby reducing the performance of the valve sealing. Therefore, when choosing a seal, be sure to choose a seal with elastic deformation. At the same time, pay attention to the width of the sealing surface. The reason is that the contact surfaces of the sealing pair cannot be completely matched. When the width of the sealing surface increases, the force required for sealing must be increased.
2. The specific pressure of the sealing surface
The specific pressure of the sealing surface affects the sealing performance of the valve and the service life of the valve. Therefore, the specific pressure of the sealing surface is also a very important factor. Under the same conditions, too much specific pressure will cause damage to the valve, but too little wine will cause valve leakage. Therefore, we need to fully consider the appropriateness of the specific pressure when designing.
3. The physical properties of the medium
The physical properties of the medium also affect the sealing performance of the valve. These physical properties include temperature, viscosity and surface hydrophilicity. The temperature change not only affects the slackness of the sealing pair and changes in the size of the parts, but also has an inseparable relationship with the viscosity of the gas. The gas viscosity increases or decreases as the temperature increases or decreases. Therefore, in order to reduce the influence of temperature on the sealing performance of the valve, when we design the sealing pair, we must design it into a valve with thermal compensation such as an elastic valve seat. Viscosity is related to the permeability of the fluid. When under the same conditions, the greater the viscosity, the smaller the permeability of the fluid. The hydrophilicity of the surface means that when there is a thin film on the metal surface, the thin film should be removed. Because this thin oil film will destroy the hydrophilicity of the surface and block the fluid channel.
4. The quality of the sealing pair
The quality of the sealing pair mainly refers to the selection, matching, and manufacturing accuracy of materials. For example, the valve disc and the sealing surface of the valve seat are very consistent, which can improve the sealing performance. The characteristic of many hoop waviness is its good labyrinth sealing performance.
TH Valve is a professional manufacturer of butterfly valve, gate valve, check valve, globe valve, knife gate valve, ball valve with API, JIS, DIN standard, used in Oil, Gas, Marine industry, Water supply and drainage, fire fighting, shipbuilding, water treatment and other systems, with Nominal Diameter of DN50 to DN1200, NBR/EPDM/VITON, Certificates & Approvals: DNV-GL, Lloyds, DNV, BV, API, ABS, CCS. Standards: EN 593, API609, API6D
Related news /knowledge:
Installation requirements for manual butterfly valves;
What is the positive transmission of gears;
Application of low temperature butterfly valve;
Valve flow characteristic curve and classification;