What is butt welding? (1)
Butt resistance welding (hereinafter referred to as butt welding) is a type of resistance welding method that uses resistance heat to weld two workpieces along the entire end surface at the same time. Butt welding has high
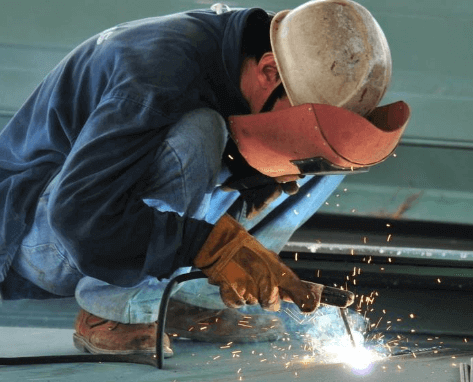
welding
productivity and easy automation, so it is widely used.
Application of butt welding:
Butt welding has high productivity and easy automation, so it is widely used. Its application range can be summarized as follows:
(1) The length of the work piece, such as the butt welding of strip steel, profile, wire, steel bar, rail, boiler steel pipe, oil and natural gas transportation pipeline.
(2) Butt welding of annular workpieces, such as car rims and bicycles, motorcycle rims, butt welding of various chain links, etc.
(3) Assembling welding of components The simple rolling, forging, stamping or machining parts are butt-welded into complex parts to reduce costs. For example, butt welding of automobile steering shaft shell and rear axle housing, butt welding of various connecting rods and tie rods, and butt welding of special parts.
(4) Butt welding of dissimilar metals can save precious metals and improve product performance. For example, the butt welding of the working part of the tool (high-speed steel) and the tail (medium carbon steel), the butt welding of the head (heat-resistant steel) and the tail (structural steel) of the exhaust valve of an internal combustion engine, the butt welding of aluminum and copper conductive joints, etc. .
Classification of butt welding:
Butt welding is divided into resistance butt welding and flash butt welding.
Resistance butt welding
Resistance butt welding is a method in which the end faces of the two workpieces are always pressed tightly, heated to a plastic state by resistance heat, and then upset pressure is quickly applied (or no upset pressure is applied and only the pressure during welding is maintained) to complete the welding.
One, resistance and heating of resistance butt welding
The resistance distribution during butt welding is shown in the figure. The total resistance can be expressed by the following formula:
R=2Rω+RC+2Reω
where Rω-the internal resistance of the conductive part of a workpiece (Ω);
Rc–the contact resistance between two workpieces (Ω);
Rω–The contact resistance between the workpiece and the electrode (Ω);
The contact resistance between the workpiece and the electrode is usually ignored due to its small resistance and far from the joint surface.
The internal resistance of the workpiece is proportional to the resistivity ρ of the welded metal and the length l0 of the workpiece extending from the electrode, and inversely proportional to the cross-sectional area s of the workpiece.
Same as spot welding, the contact resistance of resistance butt welding depends on the surface condition, temperature and pressure of the contact surface. When the contact resistance has obvious oxides or other stolen goods, the contact resistance is large. The increase in temperature or pressure will reduce the contact resistance due to the increase in the actual contact area. At the beginning of welding, the current density at the contact point is very large; after the end surface temperature rises rapidly, the contact resistance decreases sharply. When heated to a certain temperature (steel 600 degrees, aluminum alloy 350 degrees), the contact resistance disappears completely.
Like spot welding, the heat source during butt welding is also the resistance heat generated by the resistance of the welding zone. In resistance butt welding, the contact resistance exists for a very short time, and the heat generated is less than 10-15% of the total heat. But because this part of the heat is generated in a very narrow area near the contact surface. Therefore, the temperature in this area will increase rapidly, and the internal resistance will increase rapidly. Even if the contact resistance disappears completely, the heat generation intensity in this area is still higher than other places.
The harder the welding rod used (that is, the larger the current and the shorter the energization time), the smaller the pressing force of the workpiece, and the more obvious the influence of contact resistance on heating.