What is butt welding? (6)- Flash butt welding of common metals
Flash butt welding of common metals
Almost all steel and non-ferrous metals can be flash butt welded, but to obtain high-quality joints, it is necessary to take necessary process measures according to the relevant characteristics of the metal. The analysis is as follows:
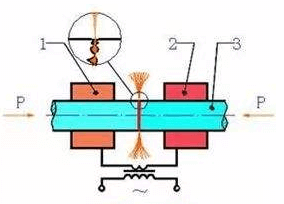
flash butt welding-schematic diagram
(1) Electrical and thermal conductivity For metals with good electrical and thermal conductivity, higher specific power and flashing speed, and shorter welding time should be used.
(2) High temperature strength For metals with high high temperature strength, the width of the temperature plastic zone should be increased and a larger upsetting force should be used.
(3) Crystallization temperature range The larger the crystallization temperature range, the wider the semi-melting zone. A larger upsetting pressure and upsetting allowance should be used to squeeze all the molten metal in the semi-melting zone so as not to stay in the joint Causes defects such as shrinkage, porosity and cracks.
(4) Thermal sensitivity There are two common situations. The first is quenched steel. After welding, the joint is prone to quenching structure, which increases the hardness and reduces the plasticity. In severe cases, quenching cracks will occur. Quenched steel usually adopts preheating flash butt welding with a wide heating zone, and adopts measures such as slow cooling and tempering after welding. The second type is metals strengthened by cold work (such as austenitic stainless steel). The joint and heat-affected zone soften during welding, which reduces the strength of the joint. Welding such metals usually uses a larger flash speed and upsetting pressure to minimize the softening zone and reduce the degree of softening.
(5) Oxidation The oxide inclusions in the joint have a serious hazard to the quality of the joint. Therefore, preventing and eliminating oxidation is the key to improving the quality of the joint. The composition of the metal is different, and its oxidative generation is also different. If the melting point of the formed oxide is lower than that of the metal to be welded, the oxide will have better fluidity and will be easily squeezed out during upsetting. If the melting point of the formed oxides is higher than that of the welded metal, such as SiO2, Al2O3, Cr2O3, etc., they must be discharged when the welded metal is still in a molten state. Therefore, when welding alloy steels containing more silicon, aluminum, chromium, and a class of elements, strict process measures should be taken to completely eliminate oxides.